Why Stepper Systems Fail—And How the Right Driver, PoStep25-256, and Rigorous Testing Prevent It
Stepper motors are the backbone of precision motion control in countless applications, from 3D printers and CNC machines to robotics and automated manufacturing systems. However, achieving optimal performance from a stepper motor requires more than just the motor itself—it demands the right driver, precise current control, and reliable testing mechanisms to ensure seamless operation.
In this comprehensive guide, we will explore four critical aspects of stepper motor systems: the role of a stepper motor driver, the advanced capabilities of the PoStep25-256, the importance of stepper motor current regulation, and the necessity of a PCB tester for validating circuit integrity. Each of these components plays a vital role in ensuring efficiency, accuracy, and longevity in motion control applications.
Whether you’re an engineer designing a new motion control system, a hobbyist building a custom machine, or a technician troubleshooting performance issues, understanding these key elements will empower you to make informed decisions. By the end of this article, you’ll have a deeper appreciation for how these technologies work together to deliver precision and reliability in stepper motor applications.
Let’s begin by examining the fundamental role of a stepper motor driver and why it is indispensable in any motion control setup.
What Is a Stepper Motor Driver and Why Is It Essential?
A stepper motor driver is a critical component in motion control systems, acting as the intermediary between a microcontroller or control system and the stepper motor itself. Unlike DC motors, which rotate continuously when voltage is applied, stepper motors move in precise increments, or “steps,” making them ideal for applications requiring accurate positioning. However, achieving this precision requires a stepper motor driver to translate low-power control signals into the high-current pulses needed to move the motor’s coils in a controlled sequence.
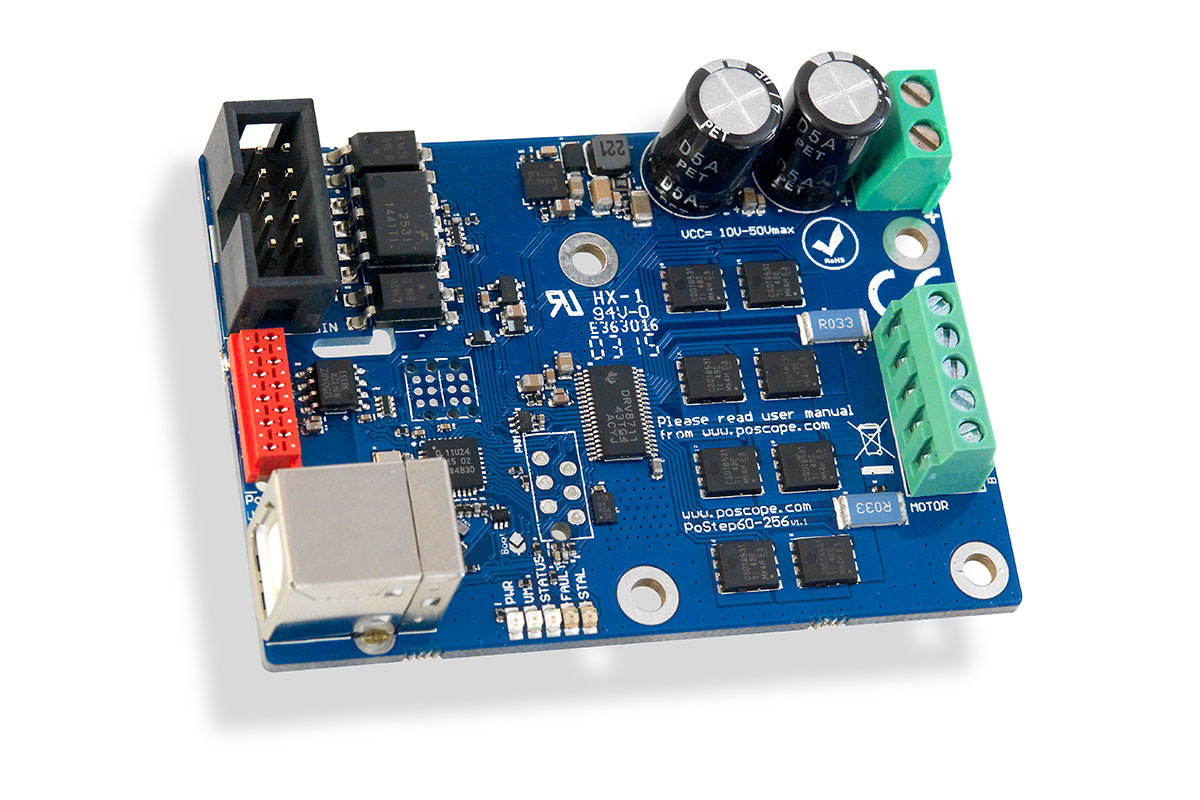
At its core, a stepper motor driver regulates power delivery to the motor’s windings, ensuring smooth and precise movement. Without a driver, a stepper motor would not receive the properly timed electrical pulses necessary for controlled motion, leading to erratic behavior, missed steps, or even motor stalling. The driver also manages critical parameters such as microstepping, current limiting, and decay modes, all of which influence motor performance.
One of the key advantages of using a stepper motor driver is its ability to implement microstepping, a technique that divides each full step into smaller increments for smoother operation and higher resolution. For example, a motor with 200 steps per revolution can achieve 51,200 microsteps per revolution when paired with a high-quality driver set to 256x microstepping. This level of precision is invaluable in applications like 3D printing, CNC machining, and robotic arms, where even minor deviations can lead to significant errors.
Another crucial function of a stepper motor driver is current regulation. Stepper motors draw varying amounts of current depending on load and speed, and an effective driver dynamically adjusts the current to prevent overheating while maintaining torque. Advanced drivers, such as the PoStep25-256, incorporate sophisticated current control algorithms to optimize efficiency and reduce energy waste.
In industrial and automation settings, the reliability of a stepper motor driver directly impacts system performance. A well-designed driver minimizes vibration, reduces audible noise, and extends motor lifespan by preventing electrical and thermal stress. Additionally, modern drivers often include diagnostic features, such as overcurrent protection and fault detection, which help prevent damage to both the motor and the control electronics.
Ultimately, the stepper motor driver is what transforms a simple stepper motor into a highly precise and controllable motion device. Whether in consumer electronics, medical equipment, or industrial machinery, the right driver ensures that the motor operates efficiently, accurately, and reliably—making it an indispensable component in any motion control system.
What Makes the PoStep25-256 a High-Performance Stepper Motor Driver?
The PoStep25-256 stands out as an advanced stepper motor driver designed for precision, efficiency, and versatility in demanding motion control applications. Unlike basic drivers, the PoStep25-256 integrates sophisticated features such as 256x microstepping, dynamic current control, and robust thermal management, making it a preferred choice for engineers and automation specialists. But what exactly sets this driver apart, and why is it well-suited for high-performance systems?
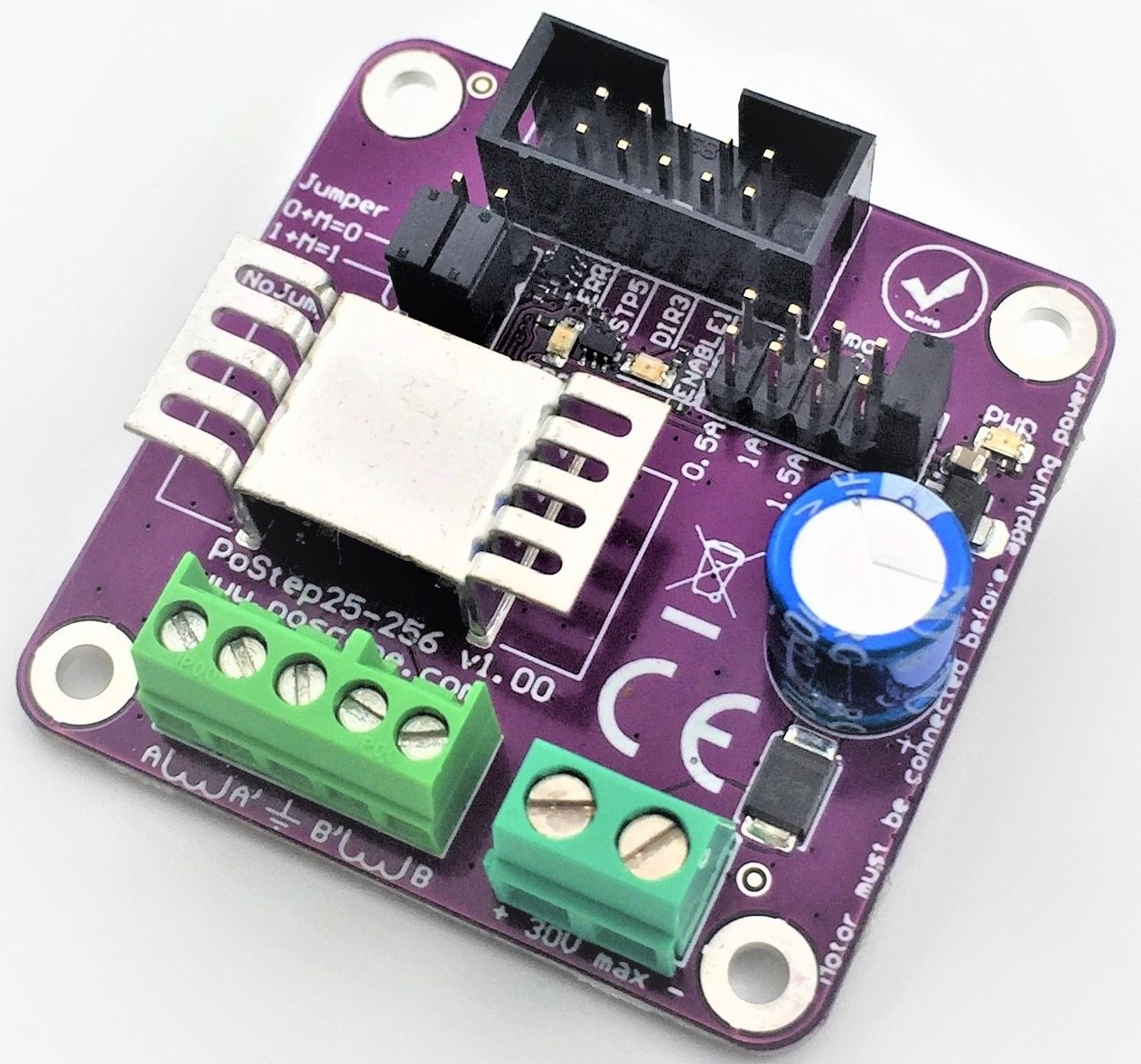
One of the most notable features of the PoStep25-256 is its ultra-fine microstepping capability. While many drivers support 16x or 32x microstepping, this model takes resolution to the next level with 256x microstepping, drastically reducing vibration and enabling near-silent operation. This is particularly beneficial in applications where smooth motion is critical, such as optical positioning systems, medical devices, and high-end 3D printers. The increased step resolution also minimizes mechanical resonance, a common issue in stepper motor systems that can lead to lost steps and reduced accuracy.
Another key advantage of the PoStep25-256 is its adaptive current control. Stepper motors often operate under varying loads, and maintaining optimal torque without overheating requires precise current regulation. The PoStep25-256 dynamically adjusts the motor current based on real-time demand, ensuring maximum efficiency while preventing energy waste. This feature is especially useful in battery-powered applications or systems where thermal management is a concern. Additionally, the driver supports programmable current limits, allowing users to fine-tune performance for specific motor types and operational conditions.
Thermal performance is another area where the PoStep25-256 excels. Many stepper motor drivers suffer from overheating under heavy loads, leading to performance throttling or even shutdowns. The PoStep25-256 incorporates advanced heat dissipation mechanisms, including optimized PCB layouts and high-efficiency power MOSFETs, to maintain stable operation even in high-temperature environments. Some variants also include thermal protection circuits that automatically reduce current if critical temperature thresholds are reached, safeguarding both the driver and the motor.
Integration and diagnostics are also simplified with the PoStep25-256. Many modern automation systems require drivers that can communicate with central controllers for real-time monitoring and adjustments. This driver supports standard control interfaces, including step/direction inputs and serial communication protocols, making it compatible with a wide range of PLCs, microcontrollers, and CNC controllers. Built-in diagnostic features, such as stall detection and fault reporting, further enhance system reliability by allowing preemptive maintenance before issues escalate.
In summary, the PoStep25-256 represents a significant leap forward in stepper motor driver technology, combining ultra-high resolution, intelligent current management, and robust thermal design. Whether used in industrial automation, precision instrumentation, or advanced robotics, this driver delivers the performance and reliability needed for the most demanding applications.
Why Is Stepper Motor Current Control Critical for Performance?
The stepper motor current flowing through a motor’s coils directly determines its torque, precision, and thermal behavior. Unlike continuous rotation motors, steppers operate by energizing their windings in precise sequences, making current regulation essential for smooth and reliable motion. Without proper stepper motor current control, systems suffer from overheating, inconsistent torque, and even step loss—issues that can derail performance in sensitive applications like CNC machining or robotic positioning.
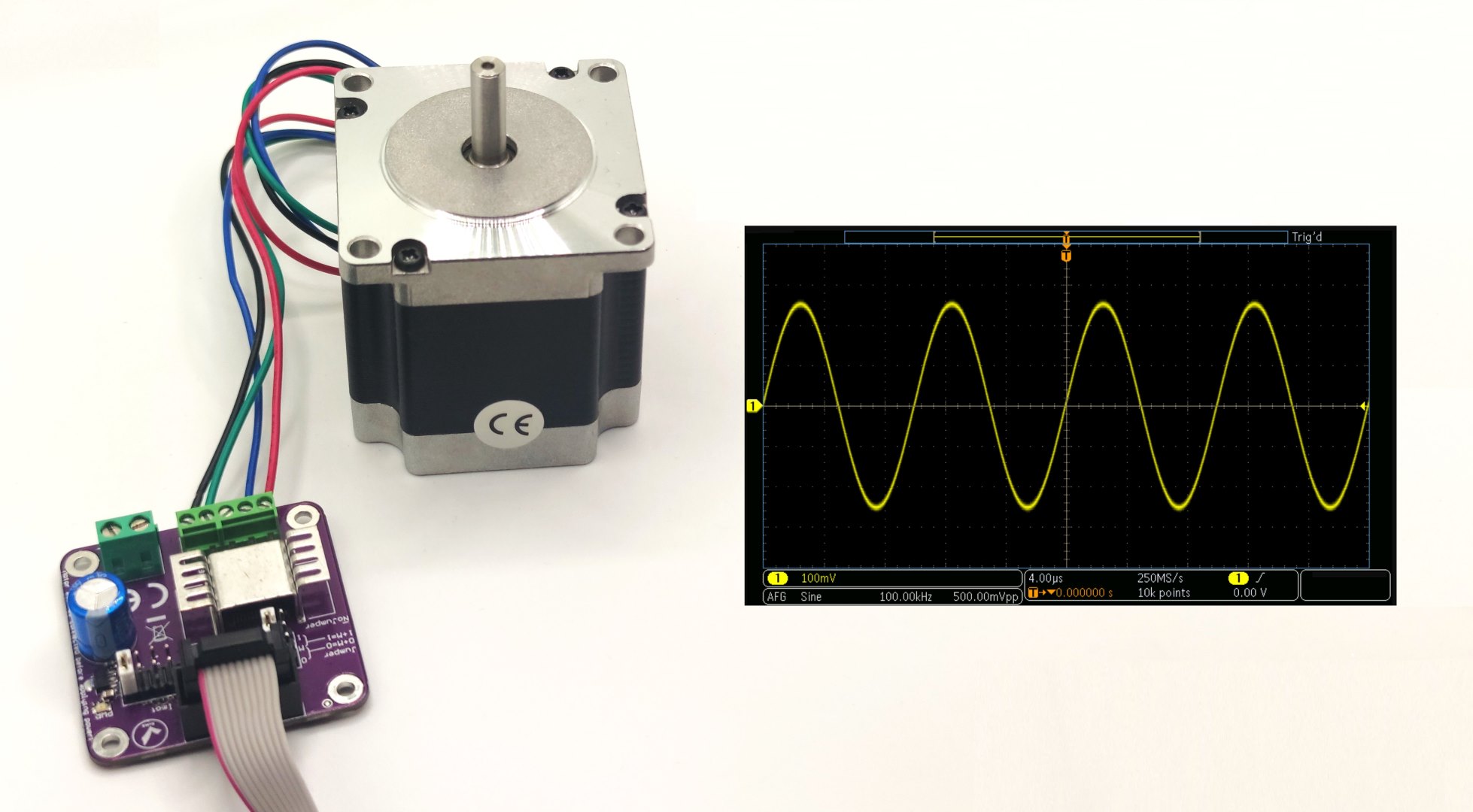
At the most basic level, stepper motor current must be carefully matched to the motor’s specifications. Applying too little current results in weak torque, causing the motor to skip steps under load. Conversely, excessive current generates unnecessary heat, degrading winding insulation and shortening the motor’s lifespan. High-quality drivers, such as the PoStep25-256, address this by dynamically adjusting current based on real-time load conditions. This ensures optimal torque while minimizing energy waste—a crucial balance in battery-powered or high-duty-cycle applications.
One of the key challenges in stepper motor current regulation is managing power dissipation. When a motor coil is energized, it behaves like an inductor, resisting sudden changes in current. Drivers use techniques like pulse-width modulation (PWM) to maintain consistent current levels without overheating. The PoStep25-256 implements advanced PWM algorithms with adjustable decay modes (slow, fast, and mixed), allowing fine-tuned control over current ripple and coil energy discharge. This reduces audible noise and vibration, particularly in microstepping applications where smooth motion is paramount.
Another critical aspect of stepper motor current control is adaptive tuning. In many systems, load requirements fluctuate—for example, a 3D printer extruder encounters varying resistance as filament feeds. Fixed-current drivers either waste energy or risk underpowering the motor during peak demands. The PoStep25-256 overcomes this with sensorless load detection, automatically scaling current to match mechanical resistance. This not only improves efficiency but also prevents overheating during prolonged operation, a common failure point in poorly regulated systems.
Thermal management is intrinsically linked to stepper motor current settings. Excessive current generates I²R losses (heat proportional to current squared), which can overwhelm a motor’s cooling capacity. Advanced drivers mitigate this with temperature monitoring and current rollback features. For instance, if the PoStep25-256 detects overheating via onboard sensors, it temporarily reduces current to safe levels while maintaining position hold—a vital failsafe in mission-critical automation.
Ultimately, mastering stepper motor current control means balancing torque, efficiency, and thermal limits. Whether optimizing a desktop CNC mill or a high-speed pick-and-place robot, precise current regulation ensures reliable performance without compromising motor longevity. In the next chapter, we’ll examine how a PCB tester validates the integrity of driver circuits, ensuring these sophisticated current control mechanisms function flawlessly from prototype to production.
How Does a PCB Tester Ensure Reliability in Stepper Motor Systems?
A PCB tester plays a vital role in guaranteeing the performance and longevity of stepper motor control systems by verifying the integrity of printed circuit boards before they enter operation. Given that even minor flaws in a PCB—such as short circuits, open traces, or faulty solder joints—can lead to catastrophic failures in motor drivers like the PoStep25-256, thorough testing is non-negotiable. But how exactly does a PCB tester work, and why is it indispensable in manufacturing and maintenance workflows?
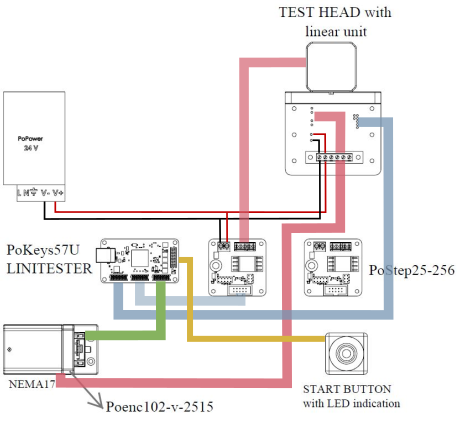
At its core, a PCB tester examines electrical continuity, insulation resistance, and component functionality across a circuit board. For stepper motor drivers, this means ensuring that power delivery circuits can handle the required stepper motor current without voltage drops or excessive heat buildup. Advanced testers automate this process, applying simulated loads to the PoStep25-256 and measuring responses to detect anomalies like unstable current regulation or signal distortion. By catching these issues early, manufacturers prevent field failures that could result in motor stalling, missed steps, or even damage to connected machinery.
One of the most critical tests performed by a PCB tester involves validating the driver’s current control circuits. Since the PoStep25-256 relies on precise PWM modulation to regulate stepper motor current, any deviation in component values—such as a degraded MOSFET or a drifted sense resistor—can disrupt performance. Automated test fixtures apply dynamic current profiles while monitoring feedback signals to ensure the driver maintains accuracy across its full operating range. This level of validation is especially crucial in safety-critical applications like medical robotics or aerospace actuators, where reliability is paramount.
Beyond electrical testing, modern PCB testers also inspect soldering quality and mechanical integrity. Poor solder joints on current-carrying traces can overheat under high stepper motor current, leading to intermittent connections or outright failures. Techniques like automated optical inspection (AOI) and X-ray imaging identify hidden defects such as voids or cold solder joints, which might otherwise go unnoticed until the driver fails in the field. Additionally, boundary scan testing verifies digital communication lines between the PoStep25-256 and its host controller, ensuring commands are transmitted without errors.
In maintenance and repair scenarios, a PCB tester serves as a diagnostic powerhouse. When a stepper motor system malfunctions, technicians use these tools to isolate faults—whether a blown capacitor on the driver board or a degraded connection in the power supply stage. By comparing test results against baseline performance data, they can quickly pinpoint whether the issue lies with the PoStep25-256, the motor itself, or an external control signal. This reduces downtime in industrial settings, where unplanned outages can cost thousands per hour.
Ultimately, a PCB tester is more than just a quality control device; it’s a safeguard against the cascading failures that can arise from undetected PCB flaws. From prototype validation to production-line checks and field servicing, these tools ensure that every stepper motor driver—whether a budget model or a high-end PoStep25-256—delivers consistent, reliable performance.
In the concluding section, we’ll synthesize how stepper motor drivers, the PoStep25-256, current control, and PCB testing interconnect to form robust motion control systems.
Precision in Motion: The Synergy of Drivers, Control, and Testing
The seamless operation of any stepper motor system relies on the careful integration of four critical elements: a high-performance stepper motor driver, an advanced controller like the PoStep25-256, precise stepper motor current regulation, and rigorous validation via a PCB tester. Together, these components form a cohesive ecosystem where precision, efficiency, and reliability are not optional—they are imperative.
The stepper motor driver serves as the command center, translating digital signals into physical motion. Without it, even the most robust motor would lack the intelligence to move with accuracy. The PoStep25-256 elevates this function further, offering unparalleled microstepping resolution and adaptive current control—features that eliminate vibration, reduce noise, and extend operational life. These capabilities prove indispensable in applications where smooth motion and positioning accuracy are non-negotiable, from automated manufacturing lines to delicate laboratory equipment.
Equally vital is the management of stepper motor current, which dictates torque, thermal performance, and energy efficiency. Too little current results in weak, unreliable movement, while excessive current leads to overheating and premature failure. The PoStep25-256 addresses this challenge with dynamic current tuning, ensuring optimal power delivery across varying loads. This intelligent regulation not only enhances performance but also minimizes energy waste—a crucial consideration in sustainable design and battery-dependent systems.
Yet, even the most sophisticated driver is only as reliable as the PCB that hosts it. This is where the PCB tester becomes an unsung hero, scrutinizing every trace, component, and solder joint to prevent latent defects. By validating electrical integrity and thermal resilience, these testers ensure that the PoStep25-256 and its supporting circuitry can endure the demands of real-world operation. Whether in prototyping or mass production, this step mitigates risks that could otherwise lead to costly recalls or operational failures.
In closing, the interplay between these technologies underscores a fundamental truth: excellence in motion control is systemic. It requires not just individual excellence in components like the stepper motor driver or PoStep25-256, but also harmony across design, power management, and quality assurance. As industries push toward greater automation and precision, mastering these elements will separate the adequate from the exceptional—enabling innovations that are as reliable as they are revolutionary.
From the workshop to the factory floor, the lessons are clear. Invest in superior drivers. Prioritize intelligent current control. Never compromise on testing. The result? Systems that move not just with precision, but with purpose.